Why a Connected Workflow is Important in Collision Repair
-
Written by David McCreight
-
Published on June 18, 2025
-
Category: Productivity and Efficiency
Collision repair has come a long way from the days of simple tools and manual labor. Today, it's a highly technical process that depends on advanced equipment and digital solutions to increase speed and precision. But technology alone isn’t enough—having an organized, connected system is key. A connected workflow links every part of the repair process, ensuring smooth communication, efficient operations, and consistent results. In this article, we’ll discuss connected workflow in collision repair and why it's critical for scalable, efficient operations.
Scalability
A scalable workflow not only enhances overall productivity but also plays a key role in boosting employee morale. When processes are efficient and well-organized, team members can focus on their tasks without unnecessary stress or confusion, leading to a more positive and motivated work environment.
Enhanced Communication
Effective communication is an integral part of running a collision repair shop. It allows employees to work more efficiently and eliminates inefficiencies that can lead to customer frustration, delays, lost work time, and lost business. By having enhanced communication, employees are on the same page and can achieve better customer satisfaction as a result.
Inventory and Parts Management
A connected workflow enables more effective management across all areas of a collision repair shop. It also ensures consistent tracking of parts and inventory, reducing delays and keeping operations running smoothly.
Compliance and Documentation
A connected workflow helps with documentation and compliance by streamlining how information is captured, stored, and accessed across the entire repair process. When all systems and tools are integrated, compliance checklists can be automatically updated, documentation can be digitally logged in real time, and records are easier to retrieve for audits or inspections. This reduces human error, ensures consistency, and makes it much simpler for a collision repair shop to stay aligned with regulatory standards.
Integration With Insurers and OEMs
A connected workflow makes it easier for collision shops to manage every step of the repair process from start to finish. By integrating systems and tools, it saves time, reduces manual effort, and creates a smoother, more efficient experience for both staff and customers.
At Collision Resources, our CR Visual Production Manager™ is an advanced auto body software that allows everyone to visualize the production process and maintain a connected workflow. CR Visual Production Manager™ is highly customizable and intuitive, allowing everyone involved in the process to see repairs in one easy solution. For more information about our auto body shop software, contact us today!
Subscribe to Our Newsletter
Interested in receiving more tips delivered directly to your inbox?
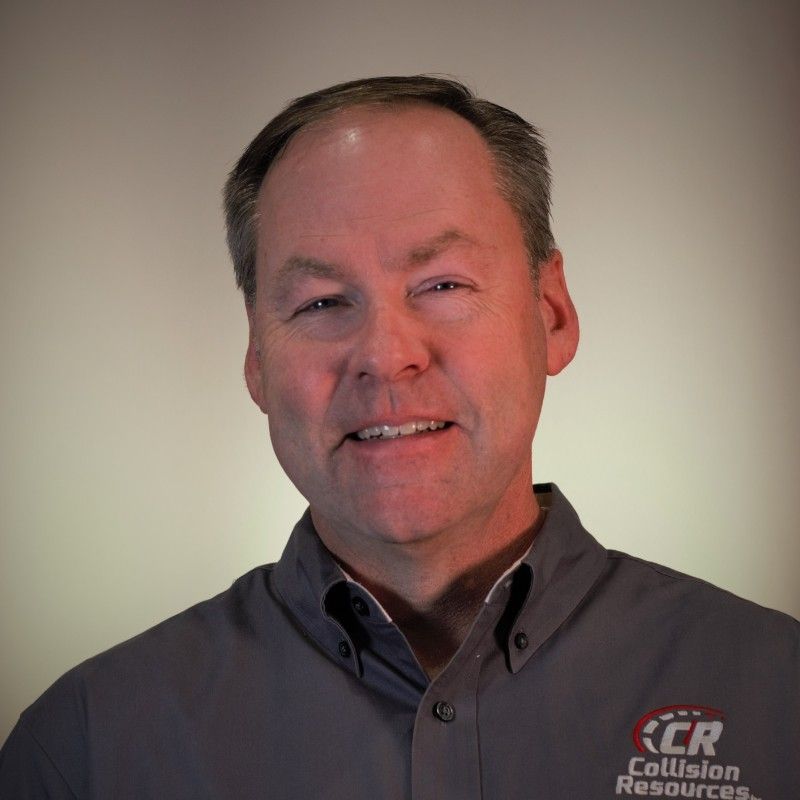
David McCreight is the Owner of Collision Resources and serves as President. Ultimately, David is categorically passionate about assisting auto body shop owners and managers to define and exceed their goals.